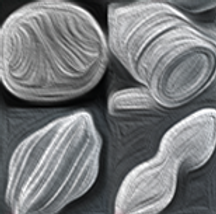
KAIST Nuclear and Quantum Engineering
Radiation Materials and Nanomechanics Lab.
Nanomechanics
Nanomechanics is a subfield of mechanics, materials science and nanotechnology focused on understanding physical or biological phenomena associated with straining small volumes of nanometer scales.
The technological trend toward high efficiency and high performance systems pushes scientists and engineers to develop new multifunctional materials which simultaneously attain the superior properties belonging to different categories. For example, stretchable electronics requires electronic materials with enhanced elastic flexibility and fatigue endurance limit, the combination of electronic and mechanical properties. Traditionally, modification of the internal microstructures has been the most important method to control the materials properties. In this case, change in one property may result in alternation of another because many different properties might be interrelated through the modified microstructure, which, in turn, makes multifunctional optimization extremely hard.
Recent research achievements in the field of nanomechanics points to the potential of controlling the mechanical properties without modifying the internal microstructure of materials. Mechanical behavior at the submicron scale turns out to be adjustable simply by changing the extrinsic size of the specimen, that is, the emergence of size-dependent mechanical properties at the nanoscale. This newly-discovered nanomechanical phenomenon may have at least two important implications. First, it can help us push the edge of the envelop to attain unprecedented mechanical properties close to their theoretical limits. Second, it can give us an opportunity to seamlessly combine the high mechanical performance with other functional behavior because topological variation of specimen sizes and shapes would unlikely affect the properties belonging to other categories.
Key research challenges in our lab may include the followings:
A. Structural Application Route
A1. Fundamental understanding of nanomechanical principles
A2. Design and fabrication of hierarchical structures for large scale structural applications
B. Functional Application Route
B1. Control of functional properties through straining
B2. Nano-devices under in-use strains
A. Structural Application Route
The size effect in mechanical properties of nanomaterials is generally the result of the interaction between mechanisms of mechanical processes such as deformation, fracture or fatigue and the geometric dimensions of the specimen. The goal of the research in this route is to manufacture mechanically robust materials by properly using the principles of nanomechanics to determine the optimal sizes and shapes of materials yielding the best mechanical performance. The results of this research will give us completely new idea to make the unconventional structural materials such as flexible bulk ceramics (Fig 1) or lightweight and high strength metals.
A1. Fundamental understanding of nanomechanical principles
In the past few years, it has been demonstrated that mechanical behavior of nanomaterials may not be explained using conventional mechanics theories. Some examples include the exhibition of smaller-is-stronger trend in metals or transition to flaw-insensitive failure in brittle ceramics. At a highly conceptual level, those unique properties stem from interference between characteristic length of an underlying process and extrinsic dimensions of specimen, but concrete understanding of such interplay is still unreached. The research in this section will mainly focus on understanding the mechanisms of mechanical processes in the nano-sized samples and establishing the fundamental nanomechanics laws. This work will requires complementary study using both of the computational and experimental methodologies, which include atomistic and multiscale simulations to obtain the atomic level resolution of the underlying processes and nanomechanical testing in the electron microscopes to observe the stress-induced microstructural evolutions. Theoretical formulation will follow to build the fundamental nanomechanical principles. The outcome of this basic research will serve as a solid foundation for other topics wherein nanomechanical analyses will play the critical role.
A2. Design and fabrication of hierarchical structures for large scale structural applications
While some unprecedented properties of nanomaterials are only attainable with nanometer-sized extrinsic dimensions, integrating them into larger scale without losing their superior properties will broaden their applicability to more general structural applications. One of such methods is constructing multiscale composite, cellular or hierarchical structures whose dimensions span from nano to macro. Here, the geometry of each hierarchical level must be properly determined so that the superior properties emergent at the nanoscale can be intactly integrated into the macroscopically-available scale. Architecturally-designed hollow ceramic nanotruss shown in Figure 2 exemplify one possibility, where the geometric sizes range from hollow tube wall thickness, ~80 nm, up to the edges of whole specimen, >100 microns. Originated from the thin wall thickness, these materials exhibit novel properties such as extremely lightweight, high strength and large flexibility (See the movie).
Based on the fundamental nanomechanical principles, the research in this section also requires us to topologically optimize architectures and develop low-cost physical and chemical fabrication techniques for such structures. So, making large-area 3D nano-architecture having optimized geometric conditions in a short time is one of our research.
B. Functional Application Route
The idea of topological control of the mechanical properties via geometric modification of the specimen's sizes and shapes without involving microstructural alternation would also provide the innovative method to seamlessly endow mechanical robustness (e.g. high strength, fracture toughness or fatigue lifetime) to the functional materials to create the better multifunctional materials. The applications of this research may include enhancement of functional performance via mechanical perturbation, the development of flexible devices in which mechanical stability and high functionality should be simultaneously pursued, or understanding of biological materials where the functional and biochemical performance is strongly correlated with mechanical stiffness. The result of this research will lead us to the possibility to synthesize new multifunctional materials attaining unusual set of properties.
B1. Control of functional properties through straining
Functional properties of crystalline solids, such as electronic, optical, magnetic or thermal, are strongly influenced by the crystallographic symmetries of constituent atoms. Under the elastic strains, the atoms in the crystal rearrange themselves to minimize the potential energy, resulting in shifting or warping of the k-space band gap structure. In other word, new crystallographic symmetries can be formed as a result of elastic strains, offering the possibility to tune the functional properties by mechanical straining. One important condition to utilize this strategy is that the crystals must sustain high enough elastic strains without failing, hardly achievable in conventional brittle materials to which most of the inorganic semiconductors belong. However, new nanomechanical principles that enables to drastically increase materials' resistance to failure (e.g. up to ~15% strain for brittle ceramics) will help us enlarge the elastic limits wherein the mechanical tuning of functional performance could have the practical implications.
This research will require the first-principle study of electronic structure in the configurational space of the constituent atoms, atomic level determination of the changes in the crystallographic symmetries caused by the applied stresses and strains, topological design of the materials' architectures capable of supporting the required strains without failure and experimental verification of the theoretical predictions by measuring the actual properties under the applied strains. The results of this research will give us another chance to achieve the unprecedented functional performance.
B2. Nano-devices under in-use strains
Lifetime enhancement or reliability is another important intersection where nanomechanics meets the needs of functional devices. Most of modern electronic devices are under various straining conditions caused by either externally applied forces or by internal sources during operation, such as thermal, chemical or electrical. The failure of components by repetition of such straining events is the main reason of the breakdown of devices. For example, degradation of lithium batteries is usually caused by the fracture of electrodes due to the lithiation-induced volume changes during electrochemical processes. Also, there are functional applications where deformability itself is the primary consideration, e.g. stretchable electronics or flexible batteries, so understanding their stress/strain states, strength, fatigue and fracture is of primordial interest. Topologically increasing mechanical durability of materials composing such devices will give us the fundamental solution to enhance their reliability because it will enable us to seamlessly adjust mechanical properties without disturbing the original functional behavior.
This research will require us to figure out the failure mechanisms of components of the nano-devices under the in-use straining conditions and to determine the proper architectures and dimensions to ensure optimal mechanical and functional performance.
Figure. 1
Schematic illustration of flexible bulk ceramic sample with internal nano-architecture. The displayed curvature represents the theoretical maximum value attainable.
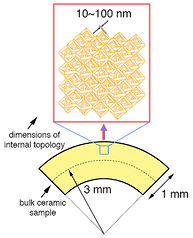
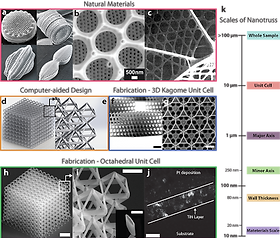
Figure. 2
Bio-inspired design and fabrication of 3D ceramic nano-architectures.
COMPRESSION EXPERIMENT ON HOLLOW CERAMIC NANOTRUSS
Crack Tolerant Mechanism at the Nanoscale of Brittle Ceramics
Improving the mechanical stability of ceramic materials to be tolerant of a sudden failure has been a major challenge in ceramic research. Brittle failure of ceramics is usually mediated by a rapid crack propagation due to the lack of intrinsic crack tolerant mechanism which requires extremely high critical stress for its activation, usually never be reached before total failure. However fracture of nanomaterials becomes insensitive to flaws when they shrink below a certain critical size. It means that, at the nanoscale, extremely high stress field which is enough to activate any fracture resisting mechanisms can be spreading out from the crack tip to the whole sample preventing the failure. By controlling the shape and size of the nanomaterials even strain hardening like behavior can be achieved in brittle ceramics imparting an fracture tolerance with rising of strengthening and toughening simultaneously. For this purpose, mainly in situ SEM/TEM nano-mechanical testing system and sample fabrication technique called Focused Ion Milling (FIB) are used to conduct the nanoscale fracture tests. Various characterization methods such as STEM-EELS and Raman, etc., are applied to investigate the detailed crack tolerant mechanism of brittle ceramics at the nanoscale, especially for diamond-like-carbon (DLC) which is isotropic, brittle and conductive amorphous ceramic. Also computational analysis such as FEM and MD are integrated with experimental results to pursue deeper understanding.
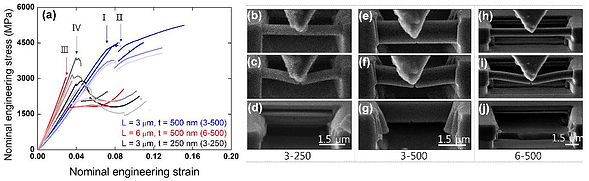
Figure 1. (a) Nominal engineering stress-strain data from fully clamped beam bending tests with pre-notches and (b-j) SEM testing images.