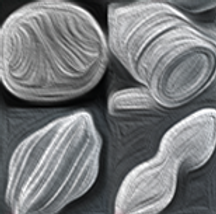
KAIST Nuclear and Quantum Engineering
Radiation Materials and Nanomechanics Lab.
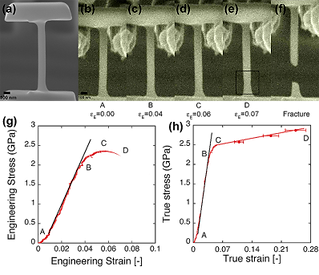
Figure. 1
100 nm wide Zr-based metallic glass sample under tensile experiment. The specimen clearly shows the increased ductility and necking behavior [2].
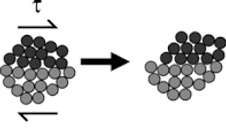
Figure. 2
Schematics showing shear transformation zone (STZ) formation in metallic glasses [4].
Radiation Materials
Radiation Effect on Amorphous Metal Alloys
Designed to operate at the elevated radiation doses and temperatures, the next generation nuclear energy systems, either fission or fusion, need to maintain their performance and functionality under the harsher environment than ever experienced before. Such requirement can be met only with a unprecedented progress in creating innovative structural materials capable of sustaining the radiation doses, e.g, up to 10 times higher than in the currently used reactors without losing mechanical stability under high temperature, pressure and corrosive conditions [1]. In the past a few decades, traditional materials-engineering methodologies, such as microstructural modification or alloying, have been successful in incrementally enhancing the radiation tolerance of structural metals and alloys used in the nuclear plants, but the demand to improve even further than now still remains. Recent advancement in nanotechnology offers another strong opportunity to fulfill such goals through controlling properties of materials utilizing the new principles only accessible at the nanometer-scale. One such example is to achieve the simultaneous increase of strength, ductility and radiation tolerance of metallic glasses (a.k.a. amorphous alloys) by scaling the extrinsic dimension of specimen down to a few tens of nanometer order (Figure 1) [2,3].
In the absence of crystallinity, the typical plasticity carriers in crystalline metals, the dislocations, are not allowed to exist in metallic glasses. Instead, the plastic deformation in metallic glasses is accommodated via collective atomic rearrangement process called shear transformation zone (STZ) (Figure 2) [4]. The activation of the STZs is largely determined by the local atomic packing density, i.e., they are more easily formed where the atoms are loosely packed. The non-uniform spatial distribution of the local atomic packing density (or equivalently excessive free volume) is possibly responsible for the ductility of metallic glasses, in which wider distribution of excessive free volumes tends to exhibit increased ductility in metallic glasses [4]. In addition, the relatively large empty spaces in those excess free volumes can possibly facilitate the trapping and self-healing of radiation damages, as is the case for several nanostructured bcc/fcc interfaces [1].
Degradation of most crystalline metals and alloys used in nuclear reactors is caused by radiation-induced nucleation of point defects, e.g. a pair of vacancy and interstitial called Frenekl pair, and the subsequent microstructrual evolution to form various types of imperfections, such as voids, bubbles, dislocations, stacking fault tetrahedra and so on [5]. As a result, the lowering of the mechanical stability of the materials has been frequently observed, including embrittlement, volumetric swelling or blistering [5]. However, because of their non-crystalline nature, the radiation-damage nucleation and evolution in nanostructured metallic glasses would have a different aspect. While the irradiation-induced collision cascade may have the similar primary effect to the amorphous solid atoms, i.e., displacement of targeted atoms from their original positions, the resulting change in the atomic structure would be the increase of the excessive free volume as opposed to the formation of Frenkel pair in crystalline metals. This is where radiation effect to metallic glasses is sharply contrasted to that of crystalline metals because the increase of the excessive free volume would contribute to the increase of ductility unlike embrittlement in crystalline metals. This line of reasoning can be supported by PI’s recent report demonstrating the ion-beam-induced increase of plasticity in electroplated nanostructured Ni-P amorphous alloys [6]. However, the energy of the incident ion particles in that experiment (30 kV) is too low to represent the irradiation condition in the nuclear reactors, which usually ranges up to a few tens of MeV orders. Therefore, to fully examine the potential use of nanostructured metallic glasses for nuclear energy systems, it is necessary to properly study the radiation effect under the condition causing comparably high damages.
Throughout this project, we propose the investigation of the radiation effects on the mechanical properties of metallic glass nanostructures. We will focus on radiation-induced atomic structure changes in the metallic glasse nanostructures and their influence on the mechanical strength and ductility. To achieve this goal, we will synergistically utilize computational and experimental approaches, which will help us elucidate the underlying mechanisms of mechanical behavior and radiational effects. The results from this research will serve as a solid foundation to develop next generation high-efficient nuclear energy system.
References
[1] Demkowicz, M. J., Bellon, P. & Wirth, B. D. Atomic-scale design of radiation-tolerant nanocomposites. MRS Bulletin 35, 992–998 (2011).
[2] Jang, D. & Greer, J. R. Transition from a strong-yet-brittle to a stronger-and-ductile state by size reduction of metallic glasses. Nature Materials 9, 215–219 (2010).
[3] Magagnosc, D. J. et al. Tunable Tensile Ductility in Metallic Glasses. Scientific Reports 3, (2013).
[4] Schuh, C. A., Hufnagel, T. C. & Ramamurty, U. Mechanical behavior of amorphous alloys. Acta Materialia 55, 4067–4109 (2007).
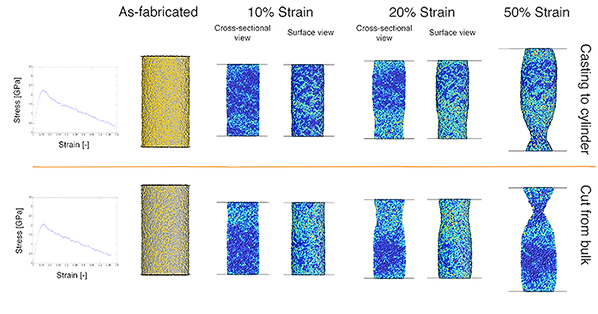
Figure. 3
Results of tensile simulation on the as-fabricated non-irradiated sample. The region between the magenta lines represents shear localization. The diameter and length of the sample are 12 nm and 16 nm, respectively (Courtesy of Prof. S. Ryu in Mechanical Engineering).